Sheet metal fabrication is the process of creating metal structures by cutting, bending, and assembling sheets of metal. This process is used to create a vast array of products, including car parts, appliances, and even aircraft parts. Sheet metal fabrication is a complex process, and it requires specialized engineers, technicians, and equipment. In this article, we will look at the main processes involved in sheet metal fabrication, the various types of sheet metal materials, and the benefits of sheet metal fabrication.
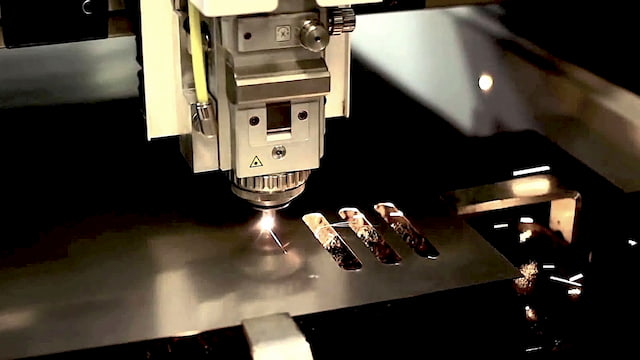
Cutting:
The first process involved in sheet metal fabrication is cutting. The sheet metal is cut into the required shape and size using a variety of cutting methods that include laser cutting, water jet cutting, and plasma cutting. Laser cutting is the most accurate and efficient method, and it is used to cut complex shapes and designs. During the cutting process, the sheet metal material used may warp or bend, so the use of high-quality materials and equipment is crucial to achieving accuracy.
Bending:
After cutting, the sheet metal is bent into the desired shape using a press brake machine. The press brake machine applies pressure to the metal sheet to bend it into the desired angle. The sheet metal may have to undergo multiple bending processes to achieve the desired shape and size. The bending process requires high accuracy and precision, and skilled technicians to operate the press brake machine.
Assembly:
In the assembly stage, the bent sheet metal parts are fitted together to create the final product. This is done using spot welding, riveting, or brazing. Spot welding is the most popular method, and it involves using a high-energy electric current to melt the metal and join it together. Riveting involves inserting metal pins through the sheet metal, while brazing involves using heat and a filler metal to create a strong joint.
Sheet Metal Materials:
Sheet metal fabrication can use a variety of materials, including aluminum, brass, copper, stainless steel, and carbon steel. Each material has its unique properties, and they are chosen depending on the desired product requirements. For example, aluminum is a popular choice for aircraft parts because it is lightweight and resistant to corrosion, while stainless steel is often used for kitchen appliances because of its durability and resistance to rust.
Benefits of Sheet Metal Fabrication:
Sheet metal fabrication has several benefits, including the ability to create complex shapes and sizes, high precision, and durability. Sheet metal products are also easy to maintain and repair, and they are recyclable and environmentally friendly. Sheet metal fabrication is cost-effective, especially for large-scale projects, and it offers quick turnaround times.
Conclusion:
In conclusion, sheet metal fabrication is a complex process that involves cutting, bending, and assembly to create various products. The process requires specialized engineers, technicians, and equipment to achieve high accuracy and precision. Sheet metal fabrication can use different materials, each with its unique properties, and offers several benefits to its users, including durability, ease of maintenance, and cost-effectiveness. If you require sheet metal fabrication services, ensure to work with a reputable and experienced company to achieve the desired product requirements.